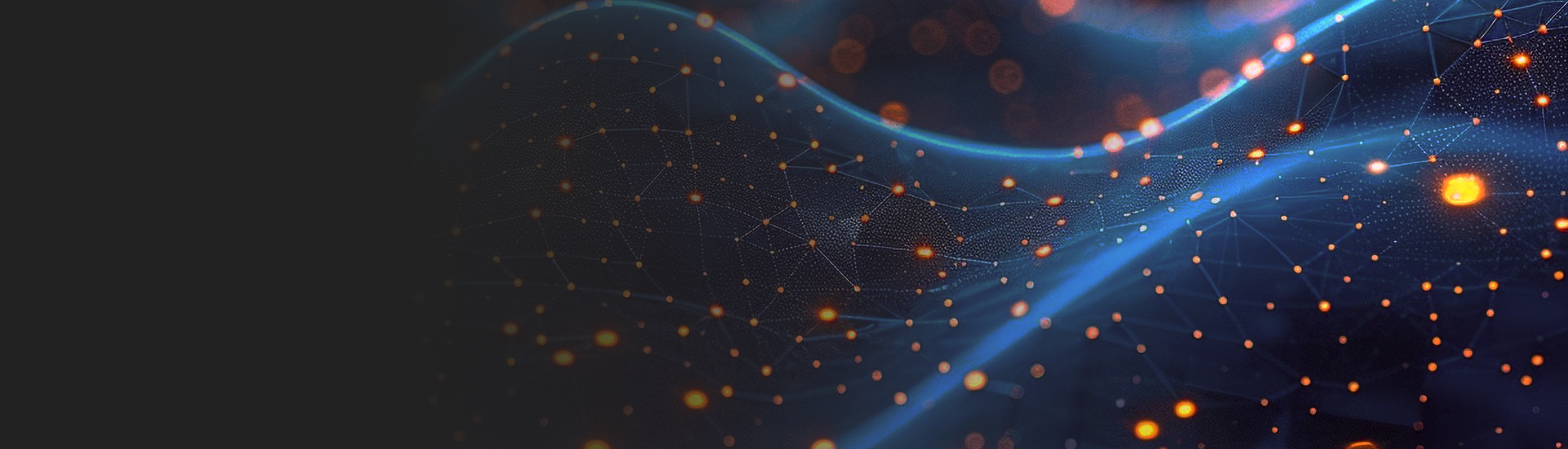
Challenges
Building an AI Inspection System for Bolt Fastening Processes
The electric vehicle parts production line has dozens of bolt fastening processes, each fastening 4 to 12 different specifications of bolts.
The existing rule-based inspection only checks the final torque value, which has limitations in detecting anomalies in the fastening process.
To transition to a smart factory, it was essential to develop and operate AI inspection models tailored to the characteristics of each process.
The Core of Real-Time AI Inspection
Ultra-Fast Quality Inspection Implemented with Edge App
The Edge App is installed on the production site PC and analyzes bolt fastening data in real time.
AI inference is completed within 0.5 seconds, providing immediate inspection results without affecting the production cycle.
It performs thousands of inspections daily with high reliability, operating independently without an external network.
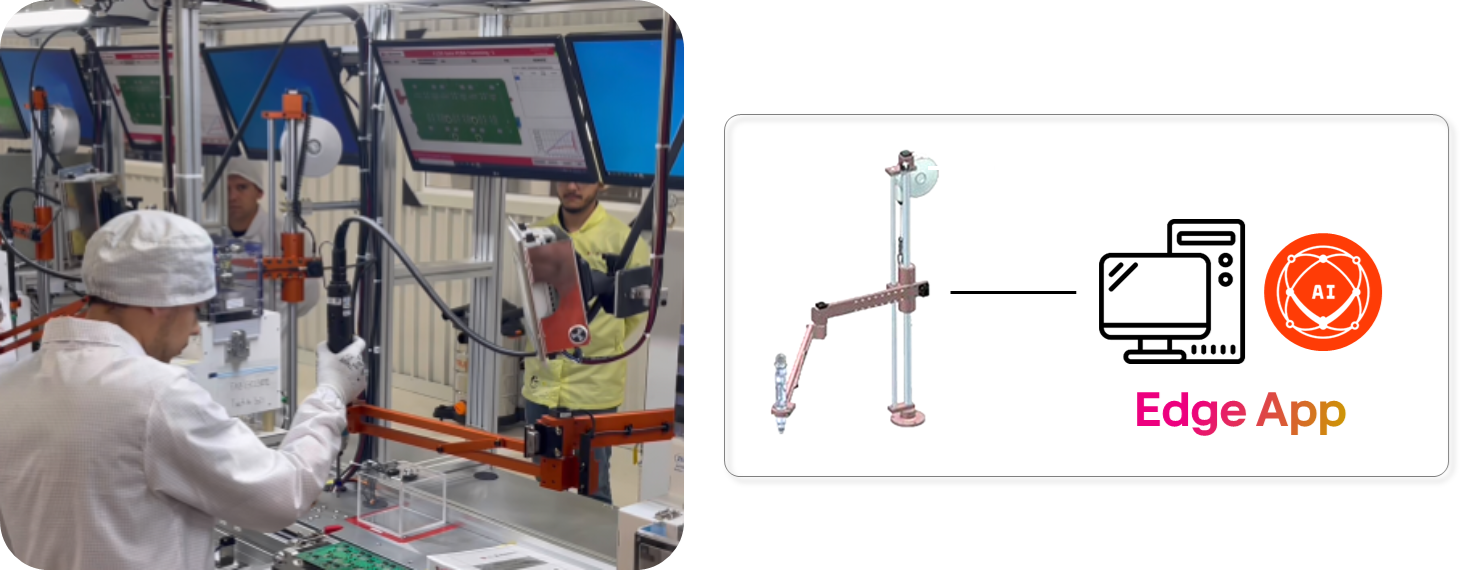
Perfect Integration with Existing Systems
The Tiny mode of Edge Viewer is fixed at the top of the screen, intuitively displaying AI inspection results without disrupting the existing work environment.
It provides immediate notifications and clear work instructions in case of defects (NG), and integrates with PLC to automatically block the movement of defective products to the next process.
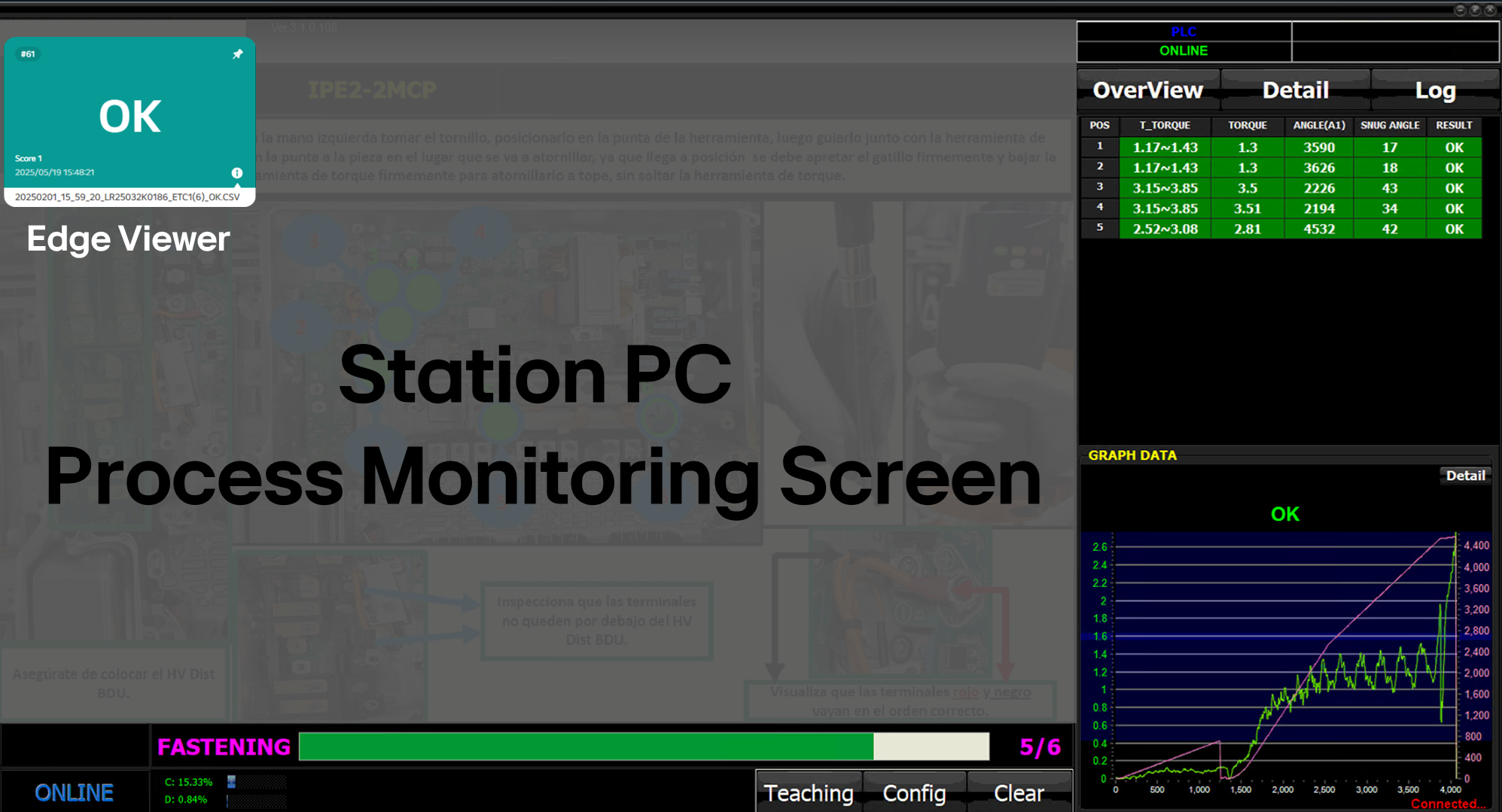
AI Operation Platform Focused on the Field
Large-Scale AI Model Management Realized with Edge Conductor
To apply AI to more than 50 bolt fastening processes, an automated management system is essential.
Edge Conductor centrally manages dozens of Edge Apps, automating the entire process from dataset creation to model training and deployment.
Field personnel can update models directly without AI expertise, enabling efficient operations centered on the field.
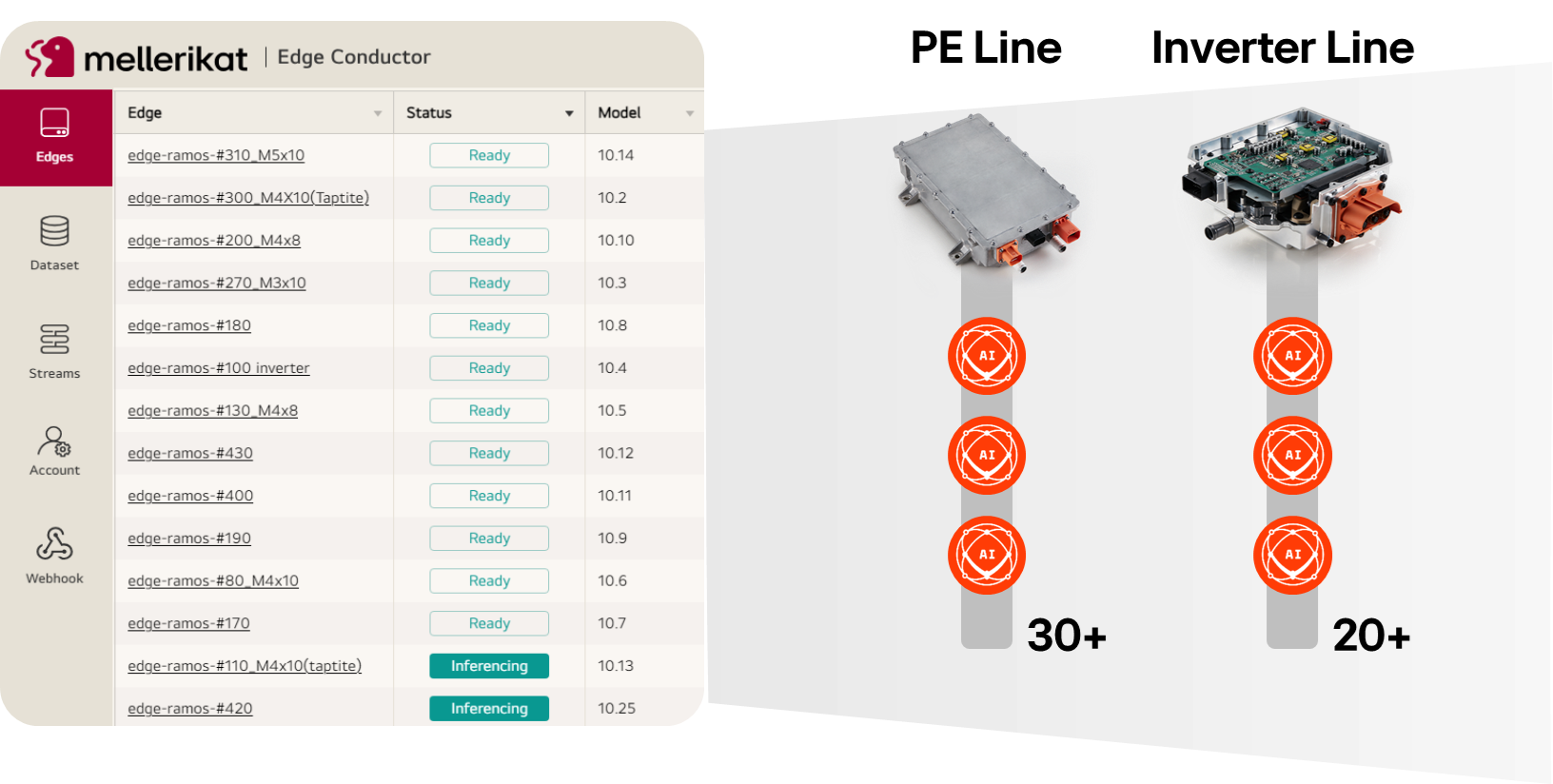
Complete Process Deployment in Just 3 Clicks
With Edge Conductor, the latest AI models can be deployed to the entire process in just 3 clicks.
Tasks that previously took days to complete manually can now be finished in minutes, allowing for continuous model updates and improvements.
Security Design Optimized for Manufacturing Environments
Safe AI Model Operation with Edge Architecture
To utilize cloud-based AI models while maintaining security in the manufacturing environment, Edge Conductor is installed in the DMZ.
It safely manages Edge Apps on the internal network while only transmitting selected data to the cloud, ensuring both security and efficiency.
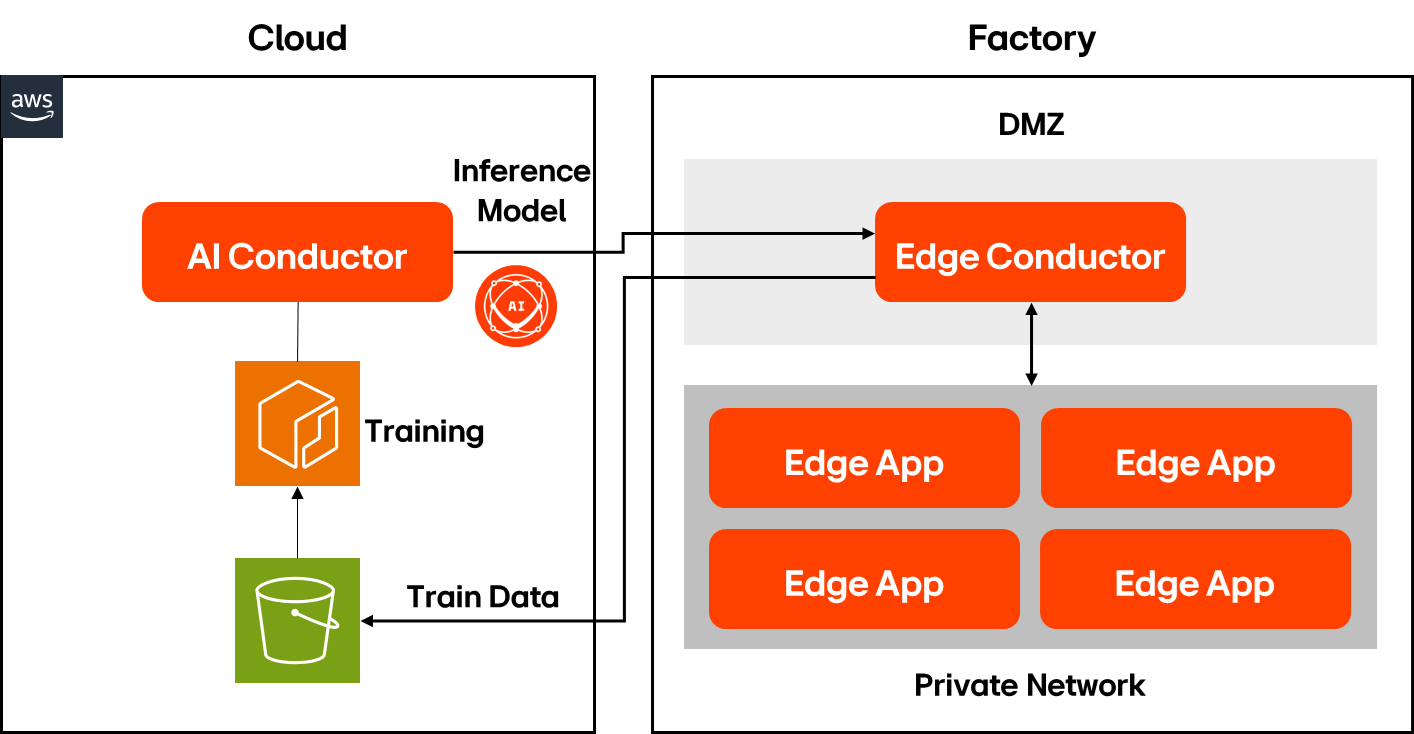
Evolution of AI Models for Bolt Fastening Inspection
Various Approaches to Find the Optimal Solution
In processes with sufficient training data, performance is validated using TCR or image-based classification models,
and to address the difficulties of data collection during the diffusion process, anomaly detection models trained only on normal data are applied.
Mellerikat supports easy validation of these various solutions to find the optimal solution for each process.
Foundation Model Optimized for Bolt Fastening Processes
Based on the data collected from validating various models, we developed a foundation model that determines the similarity of graph patterns.
This model can perform inspections immediately without process-specific training by comparing similarities with previous fastening patterns.
It automatically adapts to process changes by comparing with recent data in real time and quickly detects new defect patterns through few-shot learning.
75% Time Reduction from AI Model Development to Deployment
EDIS reduces the time required for new algorithm development and overall process deployment from one month to one week.
Through the organic collaboration of AI Conductor, Edge Conductor, and Edge App, various AI solutions can be quickly validated and deployed.
This allows for accurate detection of defects that were previously undetectable, such as bolt mixing, diagonal fastening, and foreign substances,
securing sustainable AI solutions that adapt to changes in the manufacturing environment.